Metallurgical Abstracts on Light Metals and Alloys vol.57
Strain Rate and Notch Radius Effects on Evaluating the Stress–Strain Relations Using the Stepwise Modeling Method
S. Djebien*, S. Nohara*, M. Nishida*, S. Marth**,*** and H.‑Å. Häggblad**
* Nagoya Institute of Technology
** Luleå University of Technology
*** Swerim AB
[Published in Journal of Dynamic Behavior of Materials, (2023)]
https://doi.org/10.1007/s40870-023-00397-4
E-mail: nishida.masahiro [at] nitech.ac.jp
Key Words: Strain rate sensitivity, Inverse problem, Full field measurement, Digital image correlation, Large strain
Accurate computer simulations require the selection of suitable material models and precise prediction of their parameters. In the fields of impact engineering and plastic working, stress–strain relations that include the post-necking regime up to fracture are crucial for predicting the behavior correctly. However, obtaining suitable stress–strain relations after necking requires some form of correction and adjustment for stress and/or strain. This study applies a stepwise modeling method for post-necking characterization that only utilizes the local strain field obtained from tensile experiments to precisely measure stress–strain relations at high strain rates. The effects of the notch radius of specimens on stress–strain relations were examined to measure stress–strain relations with large strain near the stress triaxiality of 1/3. The study also discusses adequate resolution for precise stress–strain measurements. Subsequently, specimens with suitable notch radius were used to measure stress–strain relations of plate specimens of aluminum alloy 2024-T3 at high strain rates. The study also examined the effects of strain rate on the flow stress and fracture strain of aluminum alloy 2024-T3.
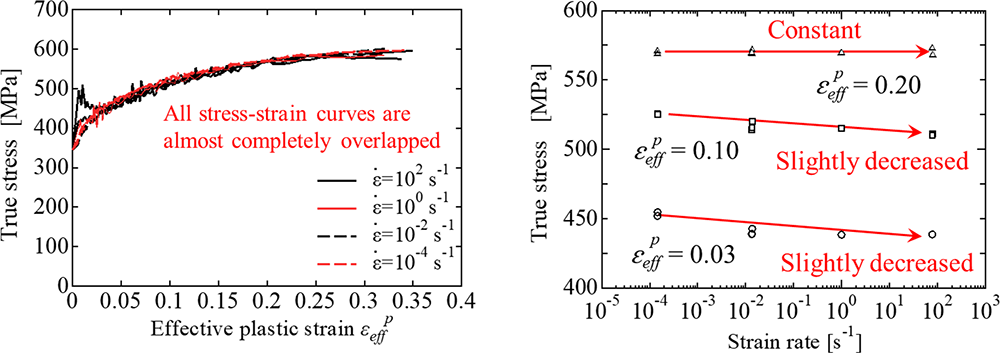
Suitable stress–strain relations after necking were obtained the step wise modeling method. Flow stress at plastic strain of 0.03 and 0.10 decrease slightly.