Metallurgical Abstracts on Light Metals and Alloys vol.57
Joining Dissimilar Laminates to Magnesium Alloy by Shot Peening
Yasunori Harada* and Yusaku Nakashima**
* Graduate School of Engineering, University of Hyogo
** Graduate Student of Engineering, University of Hyogo
[Published in Proceedings of the 25th International Symposium on Advances in Abrasive Technology, USB-No. 1017 (2023)]
E-mail: harada[at]eng.u-hyogo.ac.jp
Key Words: surface modification, shot peening, joining, magnesium alloy, wear resistance
Weight reduction is being promoted in automobiles, aircraft, and other transport equipment. Magnesium alloys, which are relatively lightweight, are attracting attention as structural metal materials. Therefore, there is a strong need to improve the wear resistance and corrosion resistance of alloys. Currently, along with alloy development, improvement is attempted by surface modification through film formation. On the other hand, shot peening has been applied to bond dissimilar thin sheets to alloy surface. While the different thin sheets are placed on the base material, the impact of steel balls causes the different thin sheet to bond to the base material. In the present study, metal laminates containing resin and ceramics were joined to improve the corrosion and wear resistance of magnesium alloys. The bondability and wear resistance of dissimilar laminates bonded to magnesium alloys were investigated. The shot peening machine was a centrifugal type, and the shot was made of cast steel with a diameter of 1 mm. The peening speed was 60 m/s and the peening time was 20 s. Bondability was evaluated by a bending test. Wear resistance was evaluated by a wear test. Wear resistance of magnesium alloys was improved by joining dissimilar laminated materials.
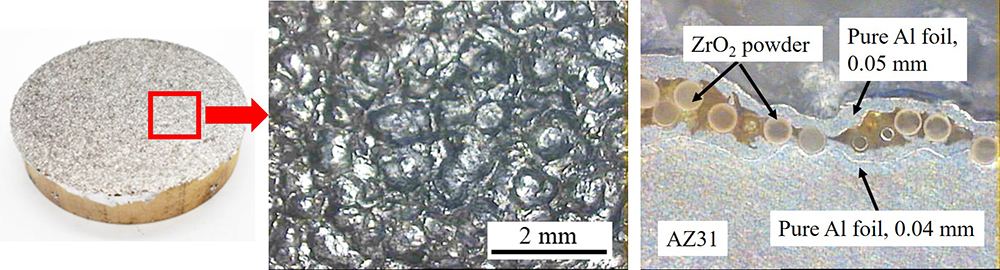
Appearance and cross section of joined workpiece after shot lining.