Metallurgical Abstracts on Light Metals and Alloys vol.57
Stiffness evaluation and numerical simulation for magnesium alloy bolted joints
Tristan Samuel Britton*, Keisuke Inoue*, Yoshinao Kishimoto*, Yukiyoshi Kobayashi* and Shogo Isobe*
* Faculty of Science and Engineering, Tokyo City University
[The proceedings of the 14th Asia-Pacific Conference on Fracture and Strength (2024), Paper ID: 5849534]
E-mail: ykishimo[at]tcu.ac.jp
Key Words: bolted joints, magnesium alloy, mechanical characteristic, finite element method
This study has clarified mechanical and dynamic characteristics of multi-material structures based on bolted joints including magnesium alloy in order to establish an analysis method. A series of hammering tests and numerical simulations were performed to clarify the relationship between the natural frequency and the clamping force, and the effect of the magnesium alloy was investigated. Compared to the other materials, the natural frequency of the magnesium alloy joint tended to increase quickly to the constant value at a lower clamping force. It considers that the low Young’s modulus of the magnesium alloy creates the real contact area increase at a higher rate even at low clamping force, because the interfacial stiffness is saturated when the real contact area becomes large enough. In addition, the natural frequency of the multi-material bolted joints was affected by the constituent materials in the case of each materials characteristics affecting the deformation shape at each vibration mode of the bolted joints. The real contact area and the material constants showed strong influences on the dynamic stiffness of magnesium alloy bolted joints. The rigidity of the constituent materials had more influence on the deformation shape with many nodes and antinodes through vibration modes.
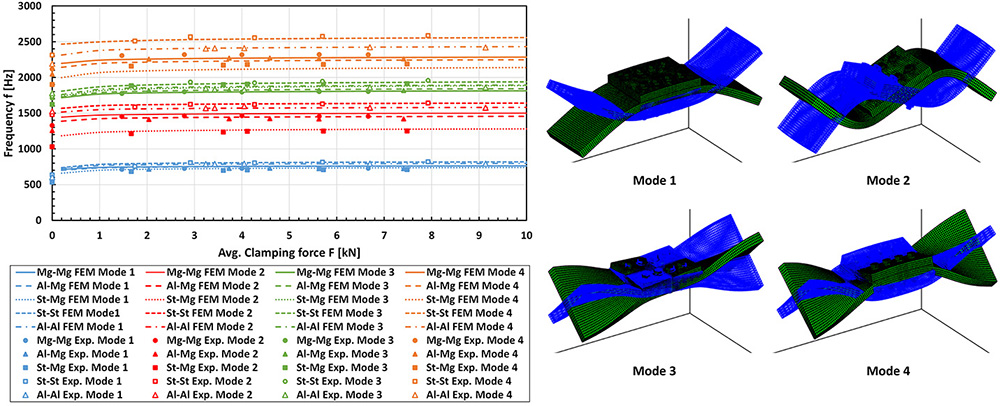
Results of hammering test and finite element simulation
(Mg = AZ31 magnesium alloy, Al = A5052 aluminum alloy, St = S50C steel)