Metallurgical Abstracts on Light Metals and Alloys vol.57
Fundamental Aspects of Wire Arc Additive Manufacturing for Aluminum Foams
Ryosuke Suzuki*, Takaya Ikeda*, Keishi Fujiwara*, Kazuya Mita**, Yoshihiko Hangai*, Hidetoshi Fujii*** and Shigeaki Kobayashi**
* Graduate School of Science and Technology, Gunma University
** Division of Mechanical Engineering, Department of Innovative Engineering, Faculty of Engineering, Ashikaga University
*** Joining and Welding Research Institute, Osaka University
[Published in Materials Transactions, Vol. 65 (2024), pp. 672-676]
https://doi.org/10.2320/matertrans.MT-M2024006
E-mail: r_suzuki[at]gunma-u.ac.jp
Key Words: Aluminum foam, additive manufacturing, wire arc welding, foaming, precursor
Additive manufacturing for open-cell aluminum foam is attracting attention because the cell morphology determined by the characteristics of the aluminum foam can be accurately controlled according to the application. However, there are few reports on the additive manufacturing of closed-cell aluminum foams. Wire arc additive manufacturing (WAAM) is a low-cost additive manufacturing method and has potential for manufacturing closed-cell aluminum foams from a wire precursor. In this study, WAAM was used to produce closed-cell aluminum foam. The precursor round bar was obtained by hot-pressing a mixture of pure aluminum powder, 3 mass% TiH2 powder, and 1 mass% Al2O3 powder. After the precursor round bar with a diameter of 15 mm was inserted into an A5052 aluminum alloy tube with an outer diameter of 19 mm and inner diameter of 15.5 mm, the assemblage was swaged to a precursor wire measuring φ1.6 × 100 mm. The WAAM equipment was based on the torch of a TIG arc welding machine that moved under numerical control. Foam formation tests were carried out with the precursor wire at a torch travel speed range from 120 mm/min to 620 mm/min. An additive foaming test was also carried out using a precursor wire measuring φ1.6 × 100 mm to investigate welding of the second layer to the first layer while the second layer was foaming. The density of the aluminum foam was measured by Archimedes’ method to calculate the porosity. The aluminum foam samples were cut perpendicular to the long axis, and cross-sections were observed with an optical microscope. For the single-layer aluminum foam formed with a TIG arc, the maximum porosity of 60% was obtained at a travel speed of 320 mm/min. A two-layer aluminum foam with a porosity of 18% and mean pore diameter of approximately 86 µm was obtained in the additive experiment. The second and first layers were bonded without forming a boundary. These results indicate that closed-cell aluminum foam was successfully produced using WAAM. However, the viscosity of the base aluminum of the precursor wire must be high to obtain a high-porosity aluminum foam with WAAM.
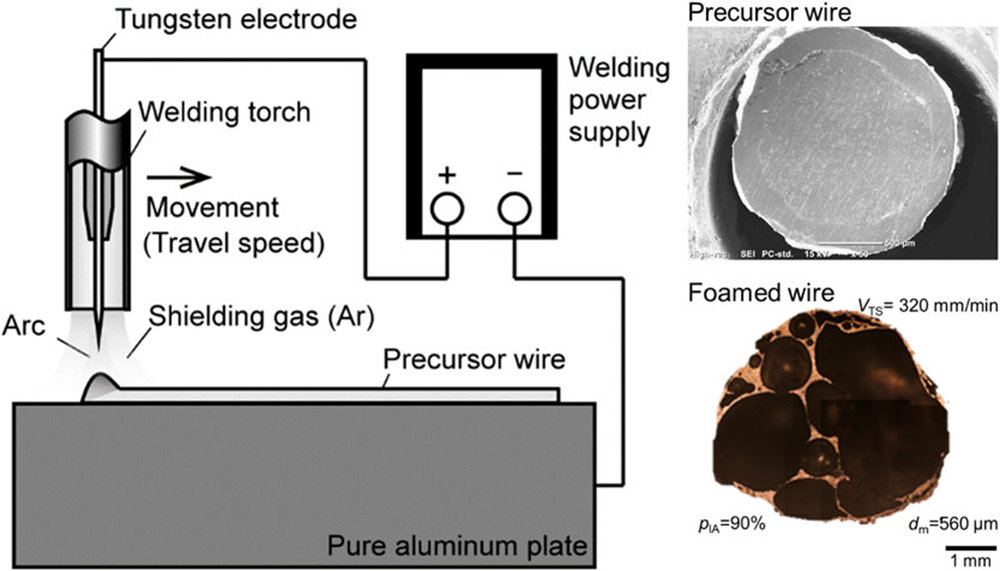
Manufacturing process of aluminum foam with wire arc additive manufacturing.