Metallurgical Abstracts on Light Metals and Alloys vol.57
Influence of Heat Treatment Time on Oxide Scale Formed on Mg Containing Al Based Alloys
Atsushi Jo*, Masaaki Kato** and Akira Yamauchi**
* Advanced Engineering Course Student, Department of Production Systems Engineering, National Institute of Technology, Gunma College
** Department of Mechanical Engineering, National Institute of Technology, Gunma College
[Published in Journal of The Japan Institute of Light Metals, Vol. 74 (2024), pp. 147-152]
https://www.jstage.jst.go.jp/article/jilm/74/3/74_740309/_article/-char/en
E-mail: ayama[at]gunma-ct.ac.jp
Key Words: Heat treatment; Al-Mg alloy; AC4B; Oxide scale; MgAl2O4
Cube specimens of AC4B aluminum alloy, Al-1%Mg, and Al-3%Mg were oxidized in air at 773 K for up to 25 h to investigate the influence of heat treatment time and Mg concentration. The original specimens and oxidation products were characterized by X-ray diffractometry, scanning electron microscopy, and X-ray photoelectron spectroscopy. SEM observation showed that the oxide scale grew thick and the surface of the oxide scale consisted of granular grain. Simultaneously, the tone color of the specimens became darker. The XRD and XPS analysis indicated that oxide scales mainly consist of MgO and MgAl2O4, and the top surface was covered with MgO. In addition, the ratio of MgAl2O4 on the surface of oxide scales tended to increase with heat treatment time. The XPS depth profile of Al-3%Mg alloy showed that oxide scale grew up to the thickness of 6 µm. The thermodynamic calculations suggested that the most stable compound on the surface of specimens is MgAl2O4 and then the kinetic factor is strongly influenced by the surface oxidation of Mg-containing Al alloys.
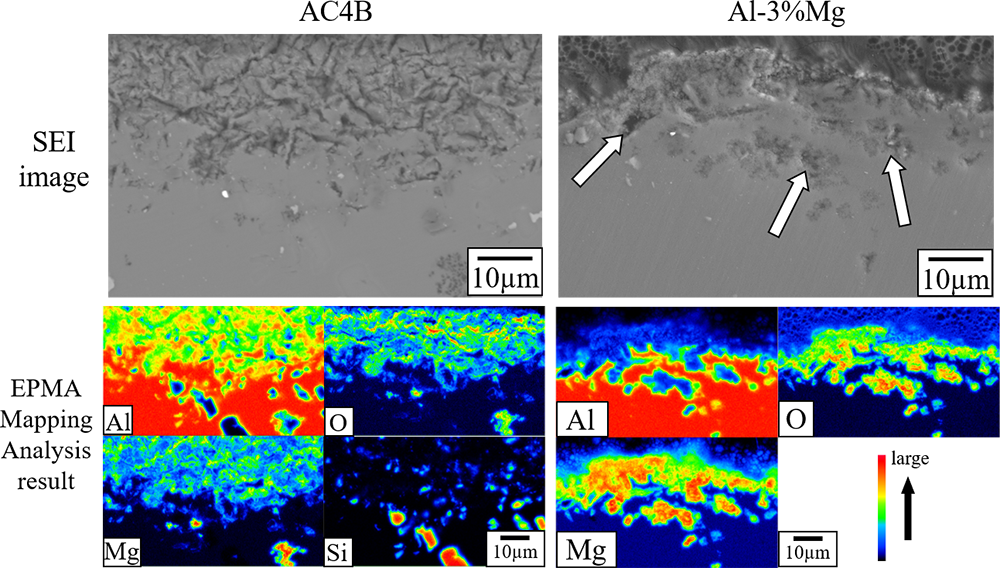
Cross-sectional SEM images and EPMA mapping of oxide scale formed on Al-3%Mg alloys and AC4B at 773 K for 25 h in an air.