Metallurgical Abstracts on Light Metals and Alloys vol.57
Pore Form and Size Dependence on Plastic Joining Characteristics of Resin/Metallic Foam by Friction Stir Incremental Forming
Ryo Matsumoto*, Shusuke Kunisawa* and Hiroshi Utsunomiya*
* Division of Materials and Manufacturing Science, Osaka University
[Published in The International Journal of Advanced Manufacturing Technology, Vol. 132, No. 1-2 (2024), pp. 717-726]
https://doi.org/10.1007/s00170-024-13405-1
E-mail: ryo[at]mat.eng.osaka-u.ac.jp
Key Words: Plastic joining, forming, Friction, Metallic foam, Resin
A metallic foam specimen was plastically joined with a resin (polymethyl methacrylate, PMMA) sheet by applying friction stir incremental forming (FSIF) process. In FSIF process, a rotating flat-ended (no probe) rod tool was pushed vertically and fed horizontally against the resin sheet which was placed on the foam. The tool operation heated frictionally the resin and deformed incrementally to the resin, while the tool operation did not deform plastically to the cellular matrix of the foam. Due to the plastic flow of the heated resin, the bottom of the resin was interlocked mechanically to the pores near the top surface of the foam. In this study, the relationship between the pore morphology (form and size) and the joining characteristics (joinability, flow thickness of the resin, and joining strength) was investigated using commercial open-cell nickel and closed-cell aluminum foams. According to the experimental investigations, the foam with small size and low depression angle of the surface pore showed better results in relation with the joining strength and the (flow thickness of the resin)/(depth of the surface pore).
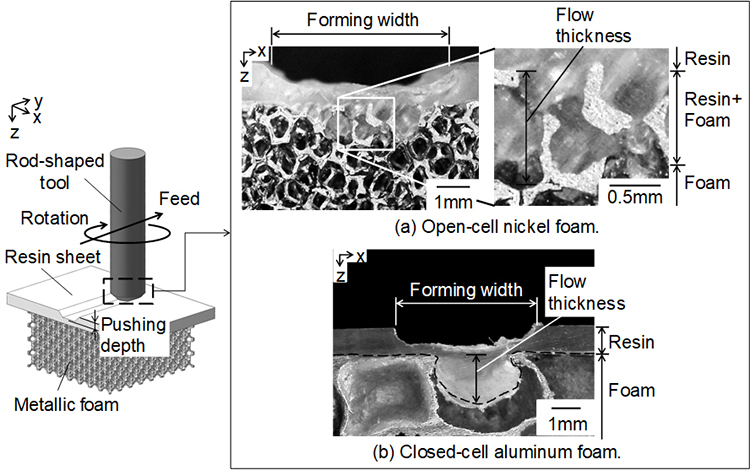