Metallurgical Abstracts on Light Metals and Alloys vol.57
Surrogate-based optimization of microstructural features of structural materials
Hiroyuki Toda1, Han Li1,2, Rafael Batres3, Kyosuke Hirayama1,4 and Hiro Fujihara1
1 Department of Mechanical Engineering, Kyushu University
2 College of Informatics, Huazhong Agricultural University
3 Campus Cuernavaca, School of Engineering and Sciences, Tecnol´ogico de Monterrey
4 Department of Materials Science and Engineering, Kyoto University
[Published in Acta Materialia, Vol. 257 (2023), 119188]
https://doi.org/10.1016/j.actamat.2023.119188
E-mail: toda[at]mech.kyushu-u.ac.jp
Key Words: Micro-tomography, Particle damage, Surrogate model, Data coarsening, Finite element simulation
This paper proposes a methodology for surrogate-based microstructural optimization of structural metals that integrates a limited number of 3D image-based numerical simulations with microstructural quantification, coarsening and optimisation processes. The support vector machine that was used had an infill sampling criterion to reduce the number of numerical trials, and the proposed methodology was found to be effective for wrought 2024 aluminium alloy with irregularly shaped particles. Appropriate objective functions were defined to assess particle damage. The number of design parameters, which quantitatively express the size, shape, and spatial distribution of particles, was initially 41, but they were reduced to four during a two-step coarsening process. The surrogate model provided highly accurate predictions, and the size, shape, and spatial distribution values of the optimal and weakest particles were successfully identified. It was shown that the optimal particle was small, spherical, sparsely dispersed, and perpendicular to the loading direction.
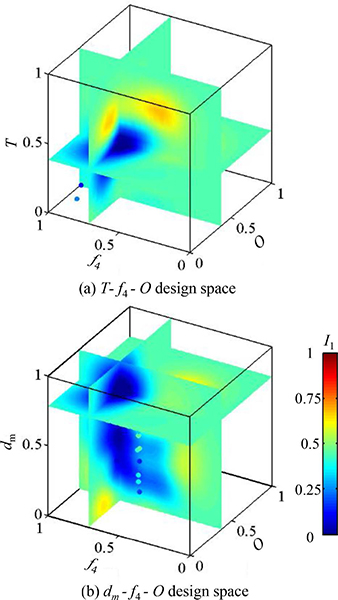
3D contour maps of the objective function I1 predicted by the surrogate model. Three design parameters were selected to show a 3D design space with the remaining parameter fixed at average values in (a) and (b) .