Metallurgical Abstracts on Light Metals and Alloys vol.57
Electrodeposition Bonding of Copper to Aluminum via Anodic Oxide Film
Yuto Tanaka*, Ryosuke Tsutsui*, Michiya Matsushima* and Shinji Fukumoto*
* Graduate School of Engineering, The University of Osaka
[Published in Quarterly Journal of the Japan Welding Society, Vol. 41 (2023), pp. 356-363]
https://www.jstage.jst.go.jp/article/qjjws/41/4/41_356/_article/-char/en
E-mail: Fukumoto[at]mapse.eng.osaka-u.ac.jp
Key Words: electrodeposition, dissimilar bonding, anodization, microstructural development, electrical resistivity, joint strength
Copper and aluminum were bonded at 298 K by electrodeposition of copper. The faying surface of the aluminum was anodized to improve the interface strength between the deposited copper and aluminum. Many tubular pores with diameters of several tens of nm were formed in the anodic oxide (alumina) film on the aluminum surface along the film growth direction, and the higher the anodic oxidation voltage, the larger the pore diameter and the thicker the wall between the pores. Electrodeposited copper and aluminum were bonded through the porous oxide film, forming a bonding interface where copper was electrodeposited in the pores in the oxide film. Although the joint was made through the oxide film at the bonding interface, it was found that there was electrical conductivity between the copper and aluminum. No intermetallic compounds were observed at the interface between the electrodeposited copper and aluminum. The fracture path depended on the microstructure of the electrodeposited Cu-Al bonding interface. High-strength joints were obtained under conditions where the micro-pores in the anodic oxide layer were filled with electrodeposited Cu. Electrodeposited copper in the tubular pores in the oxide film on the aluminum surface caused an anchoring effect at the joint interface, resulting in a sound joint with base metal fracture on the aluminum side.
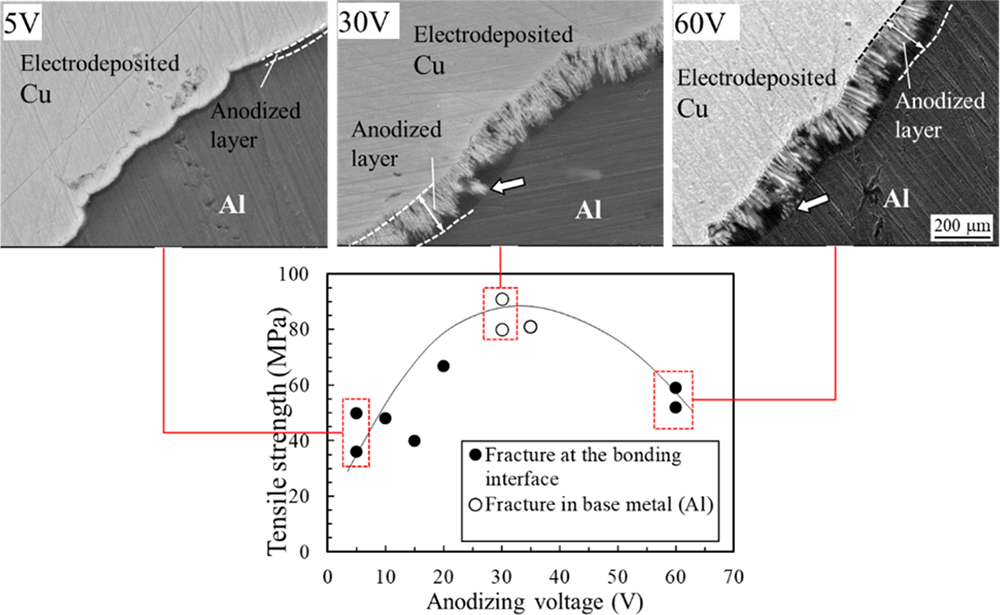