Metallurgical Abstracts on Light Metals and Alloys vol.57
The mechanical and microstructural behavior of heat treated, texture-controlled Ti-10%Mo alloys manufactured by laser powder bed fusion
Jack Peterson, Ammarueda Issariyapat, Shota Kariya, Junko Umeda and Katsuyoshi Kondoh
Joining and Welding Research Institute, Osaka University
[Published in Materials Science & Engineering A, Vol. 884 (2023), 145553]
https://doi.org/10.1016/j.msea.2023.145553
E-mail: kondoh.katsuyoshi.jwri[at]osaka-u.ac.jp
Key Words: titanium, additive manufacturing, microstructure, texture-controlled
The crystal structure of additively manufactured metals varies significantly depending on process parameters. Titanium alloy containing 10 wt% molybdenum (Ti-10Mo) shows a notable orientation-to-misoriented transition when the laser scan speed is increased from 500 mm/s to 2000 mm/s under the constant volumetric energy density of 130 J/mm³. Ti-10Mo did not exhibit significant ductility in either the as-printed or after solution treatment and air cooling, due to the presence of ω nano-precipitates and α'' martensite. However, when heat-treated at 700°C for 3 hours yielded a duplex α+β microstructure with the elongation to fracture reached 14.3%. Decreasing the orientation of the as-printed microstructure led to higher yield stress and yield stress isotropy in the heat-treated material, and strain hardening increased due to the suppression of grain rotation. Tensile plastic deformation primarily occurred in the β phase along the close-packed {110} slip system, but it was also found to occur in the α phase via the pyramidal dislocation slip. Decreasing texture suppressed grain rotation towards these slip systems, resulting in greater strain hardening. Fracture occurred along the {110}β-{0001}α interfaces of grain boundary α.
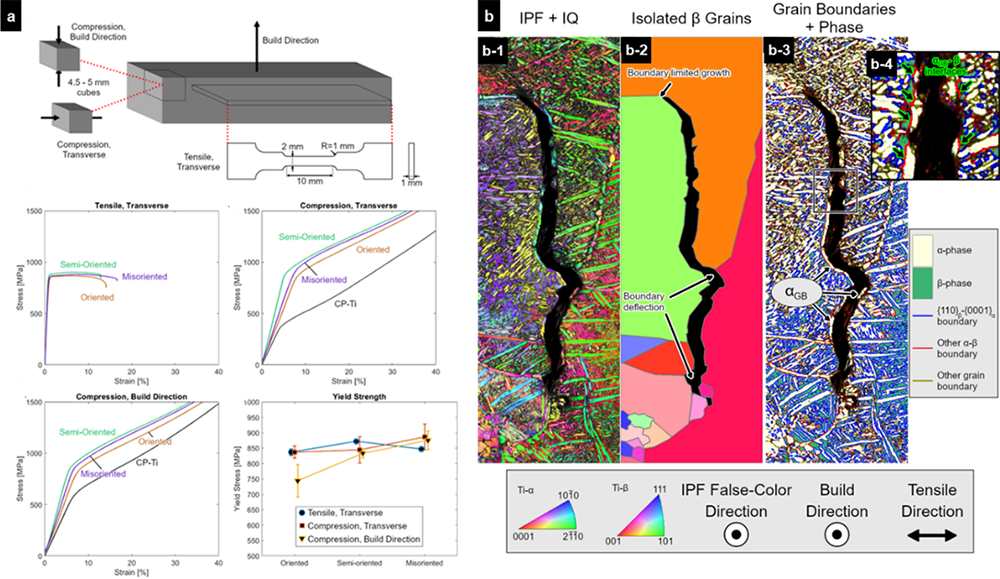
Mechanical properties of LPBF Ti-10Mo alloys after heat treatment (a) and EBSD analysis results of fractured area of sample with texture (b).