Metallurgical Abstracts on Light Metals and Alloys vol.54
Nondestructive observation of pores during press forming of aluminum foam by X-ray radiography
Yoshihiko Hangai*, Daisuke Kawato*, Mizuki Ando*, Masataka Ohashi*, Yoshiaki Morisada**, Takuya Ogura**, Hidetoshi Fujii**, Ryohei Nagahiro*, Kenji Amagai*, Takao Utsunomiya*** and Nobuhiro Yoshikawa****
*Graduate of Science and Technology, Gunma University
**Joining and Welding Research Institute, Osaka University
***Department of Mechanical Engineering, Shibaura Institute of Technology
****Institute of Industrial Science, The University of Tokyo
[Published in Materials Characterization, Vol. 170 (2020), No. 110631]
https://doi.org/10.1016/j.matchar.2020.110631
E-mail: hanhan[at]gunma-u.ac.jp
Key Words:X-ray radiography, precursor, cellular materials, press forming, X-ray computed tomography (CT), optical heating
The shaping of aluminum foam with high productivity is indispensable for the wide use of lightweight aluminum foam in various industrial fields. The precursor foaming process is one of the industrialized manufacturing processes of aluminum foam. Recently, a process for the press forming of aluminum foam during foaming of the precursor has been developed. In this study, pores during press forming were observed nondestructively by X-ray radiography. The behaviors of pores during press forming while foaming the precursor and during press forming at room temperature after the precursor had been foamed and solidified were compared. It was shown that the pores during press forming during foaming can be continuously observed nondestructively by X-ray radiography. Pores in the aluminum foam only moved and did not collapse during press forming while foaming, which indicated that ductile material flow occurred during press forming. In contrast, no flow of pores in the aluminum foam was observed during press forming of the aluminum foam at room temperature, but the cell walls collapsed and the density of the aluminum foam increased, which indicated that brittle fracture occurred during press forming. From X-ray computed tomography (CT) images of the samples, the pore structures of aluminum foam press-formed during foaming were similar to those of the aluminum foam before press forming. In contrast, the pore structures of the aluminum foam press-formed at room temperature were considerably different from those of the aluminum foam before press forming. Consequently, it was demonstrated that the press forming of aluminum foam during foaming can be used to shape aluminum foam without affecting the pore structures.
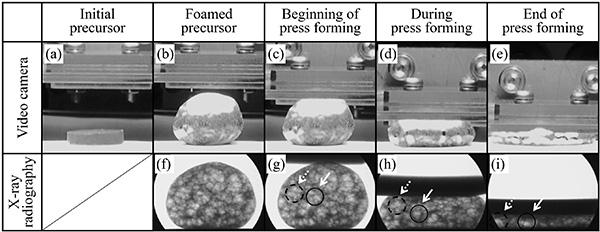
Press forming behavior during foaming obtained using video camera and by X-ray radiography system.