Metallurgical Abstracts on Light Metals and Alloys vol.54
Bending Fracture Behavior of AZ31 Magnesium Alloy Fabricated by Multi-Directional Forging
Akihiro Takahashi*, Masakazu Kobayashi** and Hiromi Miura**
*Department of Mechanical Engineering, National Institute of Technology (KOSEN), Miyakonojo College
**Department of Mechanical Engineering, Toyohashi University of Technology
[Published in International Journal of Innovations in Engineering and Technology, Vol. 19, Issue 3 (2021), pp. 8–15]
E-mail: akihiro[at]cc.miyakonojo-nct.ac.jp
Key Words:magnesium alloy, multi directional forging (MDF), bending test, fracture behavior
AZ31 Mg alloy sample was thermal-deformed by MDF at strain rate of 3 × 10-3 s-1 with varying through 90° from pass to pass and with decreasing temperature obeying a certain forging profiles. Three-point bending test was carried out at initial loading speed of 1.0 mm/min at room temperature. Fractography by SEM was carried out and typical photographs are displayed in Fig.1. Figs.1 (a) and (d) exhibit dissociation characteristics with metallurgical slip orientation for deformation in the as-extruded specimen. There are a large number of the river patterns in very different directions, the cleavage terraces and a few small dimples on the surfaces. It was suggested that a lot of large slip bands and profuse twinning were developed along to certain orientations in the grain interior in the as-extruded specimen. Micrographs in Figs.1 (b) and (c) show mostly ductile fracture surface with dense dimples in both MDFed specimens, where dimples of resembling comet shape look aligned upward (see Figs.1 (e) and (f)). The multiaxial stress state in the internal necking within the plastic region urges shear stress component. Arrows in white color near the V-notch root indicate secondary microcrack extended in vertical to the photographs. These microcracks was lead to an increase in extrinsic deformation. Therefore, it was suggested that the equivalency stress of Von-Mises stress, σ (i.e., shear strain energy) in the front of V-notch increases due to occurrence of the microcracks.
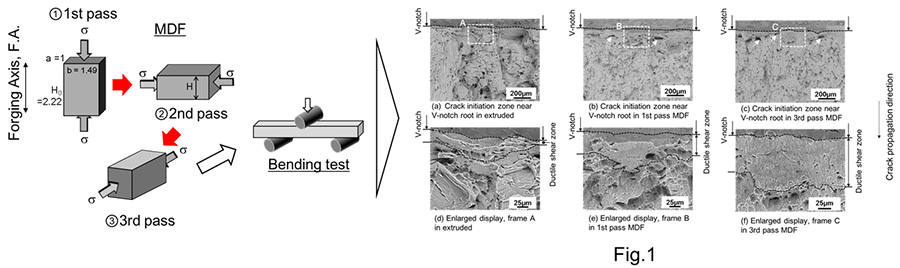
Fig.1 SEM micrographs of the fracture surfaces near V-notch root; specimens of (a) and (d) hot-extruded, (b) and (e) 1st pass MDFed, (c) and (f) 3rd pass MDFed. (d), (e) and (f) are the enlarged images of the frames A, B and C in (a), (b) and (c). Main crack propagation direction is indicated by white arrows. Areas surrounded by black-dashed lines in (d), (e) and (f) show brittle fracture manner.