Metallurgical Abstracts on Light Metals and Alloys vol.54
Residual stress induced failure of Ti-6Al-4V/Si3N4 joints brazed with Ag-Cu-Ti
filler: the effects of brazing zone’s elasto-plasticity and ceramics’ intrinsic properties
Fei Shen Ong*, Bastian Rheingans**, Kenta Goto***, Hirobumi Tobe*, Takahito Ohmura***, Jolanta Janczak-Rusch** and Eiichi Sato*
*Institute of Space and Astronautical Science, Japan Aerospace Exploration Agency (ISAS/JAXA)
**LaboratoryforJoiningTechnologiesandCorrosion,SwissFederalLaboratories for Materials Science and Technology (Empa)
***International Center for Young Scientists, National Institute for Materials Science (NIMS)
[Published in Journal of the European Ceramic Society, 41 (2021) 6319–6329]
https:// doi.org/10.1016/j.jeurceramsoc.2021.06.038
E-mail: sato[at]isas.jaxa.jp
Key Words:residual stress, ceramics, dissimilar brazing, finite element analysis (FEA), nano-indentation
The residual-stress induced failure of Ti-6Al-4V/Si3N4 joints brazed with two different Si3N4 ceramics possessing different intrinsic properties was elucidated through experimental and finite-element (FE) thermo-mechanical simulations incorporating the local elasto-plastic properties of the as-received Ag-Cu-Ti filler and the brazing zone characterized by nano-indentation. All tested joints fractured mainly from the ceramics due to residual stress, and their bending strengths increased when using Si3N4 ceramics of higher intrinsic strength. FE-analysis based on the as-received filler’s properties overestimated the nominal bending strengths by approximately 100 MPa in both joints; nano-indentation revealed that the depletion of ductile Ag-Cu phase and growth of hard Cu-Ti intermetallic compounds reduced the plastically deformable thickness after being brazed, whereby they resulted in higher residual stress in the ceramics. Finally, the validity of FE-estimated bending strengths was enhanced when considering the effective plastically deformable thickness of filler (30 µm) instead of the as-received state (50 µm).
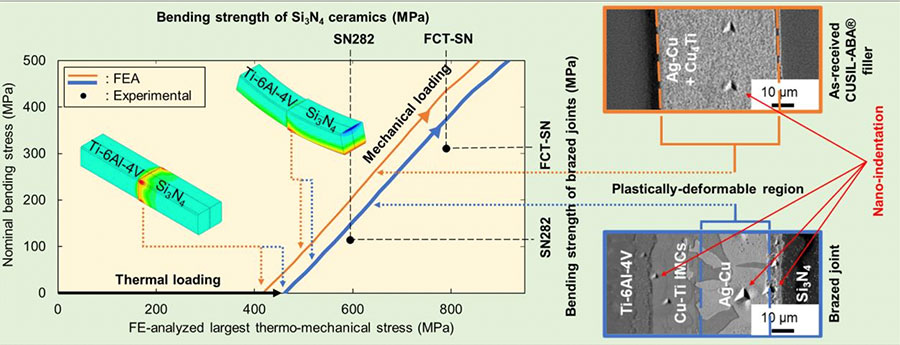