Metallurgical Abstracts on Light Metals and Alloys vol.55
Additively Manufactured and Sintered Titanium Alloys with Nitrogen Solutes
Ammarueda Issariyapat*, Tingting Song**, Patama Visuttipitukul***, Junko Umeda*, Ma Qian** and Katsuyoshi Kondoh*
*Joining and Welding Research Institution, Osaka University
**Centre for Additive Manufacturing, School of Engineering, RMIT University
***Department of Engineering, Chulalongkorn University
[Published in Advanced Powder Technology, 32 (2021), pp. 2379–2389]
https://doi.org/10.1016/j.apt.2021.05.023
E-mail: kondoh[at]wri.osaka-u.ac.jp
Key Words: titanium, core-shell structured powder, nitriding, additive manufacturing
In this study, Ti-(N) powders with a core-shell structure were prepared via a nitriding process of titanium (Ti) powders for metal additive manufacturing (AM). Nitriding of spherical Ti powders (D50=130 µm and D50=63 µm) was carried out at different temperatures from 873 K to 1373 K for 10 min. The nitriding process enabled the manufacture of a core-shell structured Ti-(N) powder, where an N-enriched shell surrounds a lower N core. The core-shell structured Ti-(N) powders were subsequently used to manufacture bulk samples by spark plasma sintering (SPS) and laser metal deposition (LMD) processes for comparison. The microstructure was characterized and discussed. LMD-fabricated Ti-N alloy samples exhibited high tensile strength (965 MPa) with good tensile ductility (7.6%) due to the homogeneous distribution of N and fine grain size. In contrast, SPS-fabricated Ti-N alloy samples using the same nitrided Ti-N powder showed much lower tensile strength (708 MPa) with essentially no tensile ductility (0.3%) due to the inhomogeneous distribution of N. LMD can allow the fabrication of strong and ductile Ti-N alloys while it is not possible by SPS.
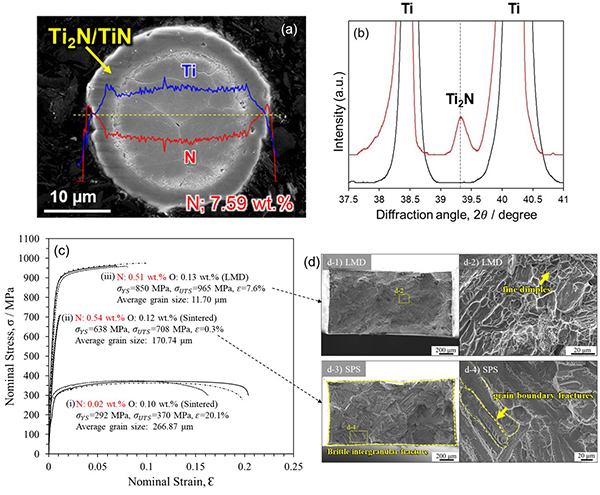
SEM-EDS (a) and XRD results (b) of core-shell structured Ti-N powder, tensile properties of Ti-N alloys fabricated by AM and PM process (c) and their fractured surfaces after tensile test (d).