Metallurgical Abstracts on Light Metals and Alloys vol.55
Strength optimization of two-step-bonded Ti-6Al-4V/Si3N4 joint with Nb interlayer via transient-liquid-phase bonding and active-metal brazing Abstract Title
Fei Shen Onga,b, Ryotaro Nishia,b, Hirobumi Tobea and Eiichi Satoa
aInstitute of Space and Astronautical Science, Japan Aerospace Exploration Agency (ISAS/JAXA)
bDepartment of Materials Engineering, Graduate School of Engineering, The University of Tokyo
[Published in Journal of the European Ceramic Society 42 (2022) 2707–2717]
https://doi.org/10.1016/j.jeurceramsoc.2022.01.039
E-mail: sato[at]isas.jaxa.jp
Key Words: Brazing, Transient-liquid-phase bonding, Ceramics, Residual stress, Finite element analysis
A novel two-step bonding of Ti-6Al-4V/Si3N4 joint was developed with Nb interlayer as residual-stress reliever via low-pressure transient-liquid-phase bonding (TLPB) of Ti-6Al-4V/Nb side prior to active-metal brazing of Nb/Si3N4 side. While 1.75 mass% of Ti in a 50-µm-thick CUSIL-ABA® filler was sufficient for sound bonding at Nb/ Si3N4 side when brazed at 1103 K for 10 min, one-step- brazed joints with bonding area of 10 × 10 mm2 were prone to failure at the Ti- 6Al-4V/Nb side due to brittle Cu-Ti intermetallic compounds (IMCs). Replacing brazing of Ti-6Al-4V/Nb side with TLPB using pure Cu and Ni foils as filler at 1213 K for 180 min eliminated the formation of brittle IMCs via homogenization of (α+β)-Ti; bending strength increased to 193 MPa with residual-stress-induced failure from Si3N4 ceramics. Finally, effectiveness of stress-accommodation via Nb interlayer and filler’s plastic flow was quantitatively verified with reasonable fidelity by finite-element analysis incorporating temperature-dependent elasto-plastic properties.
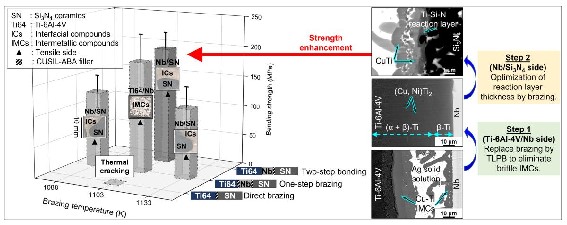