Microstructure and mechanical properties of 4045/3003/4045 aluminum alloy clad
sheet fabricated by vertical-type high-speed tandem twin-roll casting
Ryoji Nakamura1), Akari Tsutsui1), Toshio Haga2), Yohei Harada1) and Shinji Kumai3),
Kazuko Terayama4), Akio Niikura4)
1) Department of Materials Science and Engineering, Tokyo Institute of Technology
2) Department of Mechanical Engineering, Osaka Institute of Technology
3) Department of Metallurgy and Ceramics Science, Tokyo Institute of Technology
4) UACJ Corporation
4045/3003/4045 aluminum alloy clad sheets having the same thickness (6.0 mm) and clad ratio (12 %) were fabricated both by hot roll-bonding and vertical-type high-speed tandem twin-roll casting. Figure 1 shows a schematic illustration of the vertical-type high-speed tandem twin-roll caster. The clad sheets were cold-rolled to 0.17 mm in thickness, annealed at 400°C for 2 h, cold-rolled to 0.10 mm in thickness and finally subjected to heat treatment for brazing at 600°C for 3 min. Figure 2 shows an illustration of the process flow. Microstructures and mechanical properties of the clad sheets were investigated in each stage. Figure 3 shows SEM-BEI images of the cold-rolled sheets fabricated by (a) hot roll-bonding and (b) twin-roll casting. Magnified view near the interface in (a) and (b) is shown in (c) and (d), respectively. Al-Mn dispersoid particles in the core (A3003) and Si particles in the overlay (A4045) of the cold-rolled sheet with 0.17 mm thickness originating from the twin-roll casting were smaller than those originating from the hot roll-bonding. Interfaces between the core and the overlay were clearly observed in the twin-roll casting sheets. Figure 4 shows grain structure of the clad sheets after annealing. A fully recrystallized structure was observed after annealing in the sheet originating from the hot roll-bonding, while the fibrous structure still remained in the sheet originating from the twin-roll casting. Figure 5 shows stress-strain curve of the annealed clad sheets (thickness: 0.17 mm). Yield strength, tensile strength and elongation of the annealed sheet originating from the twin-roll casting were higher than those originating from the hot roll-bonding. Figure 6 shows stress-strain curves of the clad sheets after heat treatment. After the heat treatment for brazing, the tensile strength was the same in both clad sheets.
[Published in Journal of the Japan Institute of Light Metals, Vol. 64, No. 9 (2014) pp. 399-406]
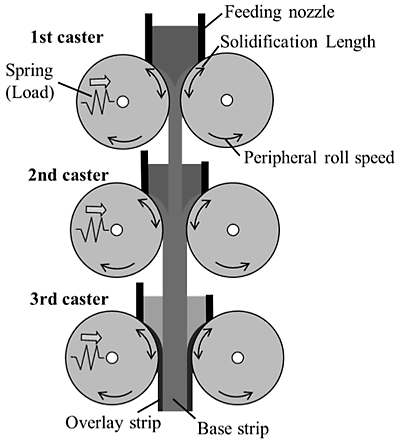 |
Fig. 1 Schematic illustration of the vertical-type high-speed tandem twin-roll caster.
|
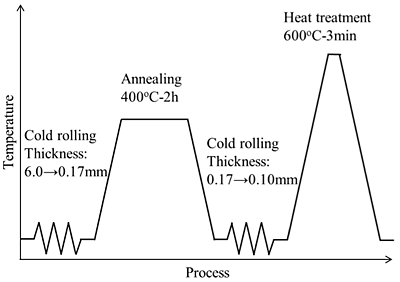 |
Fig. 2 Illustration of the process flow.
|
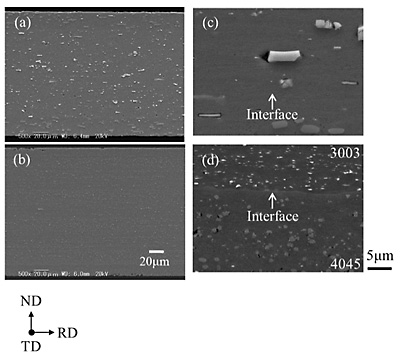 |
Fig. 3 SEM-BEI images of the cold-rolled sheets fabricated by (a) hot roll-bonding and
(b) twin-roll casting. (c) and (d) : magnified view near the interface in (a) and (c), respectively.
|
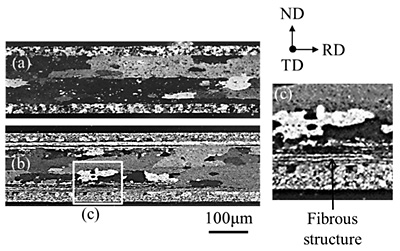 |
Fig. 4 Grain structure of the clad sheets after annealing. (a) hot roll-bonding,
(b) twin-roll casting, (c) magnified image of the framed area in (b).
|
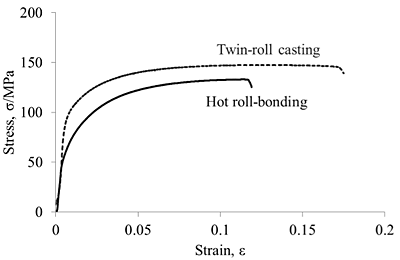 |
Fig. 5 Stress-Strain curves of the annealed clad sheets (thickness: 0.17 mm).
|
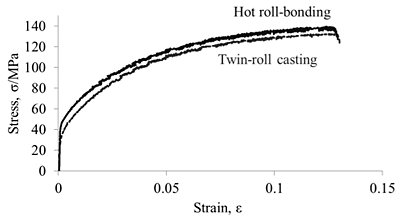 |
Fig. 6 Stress-strain curves of the clad sheets after the heat treatment for brazing.
|